Materialproduktivität verbessern – Materialeffizienz steigern
Materialproduktivität verbessern – Materialeffizienz steigern
Das Thema Materialeffizienz hat neben seiner umweltpolitischen auch eine hohe wirtschaftliche Bedeutung und ist eine herausfordernde Aufgabe für Unternehmen des industriellen Mittelstands. Die Deutsche Materialeffizienzagentur (demea) definiert Materialeffizienz als "Verhältnis der Materialmenge in den erzeugten Produkten zu der für ihre Herstellung eingesetzten Materialmenge". Materialeffizienz ist also das mengenbezogene Pendant zu der wertbezogenen Materialproduktivitätsdefinition dieses Leitfadens.
Eine höhere Materialeffizienz kann nach der Deutschen Materialeffizienzagentur durch Reduzierung des Materialeinsatzes erreicht werden, zum Beispiel durch:
- das Verringern des Ausschusses
- das Reduzieren von Verschnitt
- den verringerten Einsatz von Hilfsstoffen
- das Optimieren der Produktkonstruktion
Wenn Sie die Materialeffizienz überprüfen und verbessern, dann erhöhen Sie zugleich folgende Teilproduktivitäten:
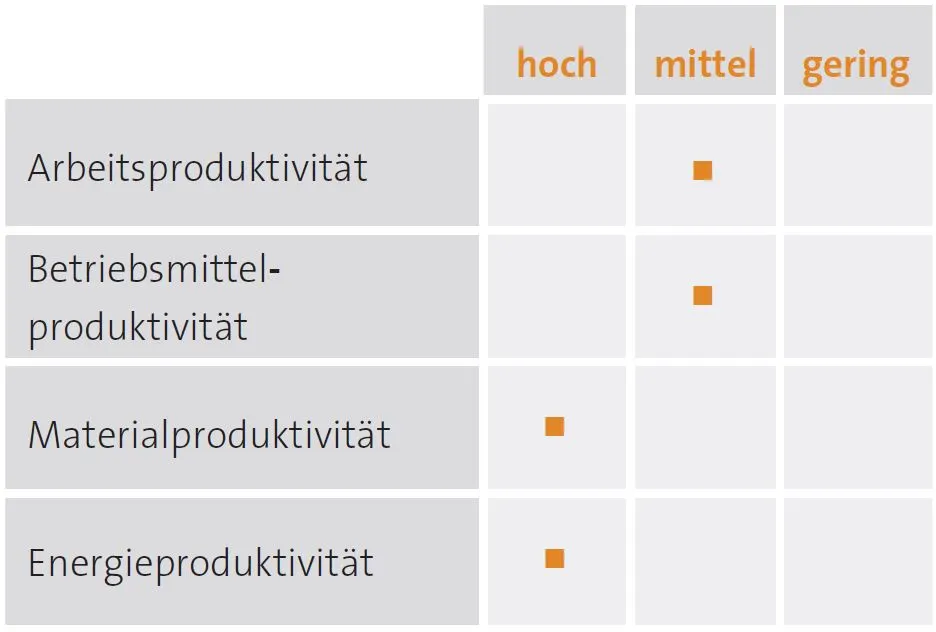
Ausgangpunkt: steigende Materialkosten und Versorgungsrisiken
Die Rohstoffpreise steigen stetig. Deutsche Unternehmen geben jährlich insgesamt 500 Milliarden Euro für Rohstoffe und Materialien aus. Laut der Deutschen Materialeffizienzagentur können durch einen effizienten Materialeinsatz rund 20 Prozent der Materialkosten eingespart werden. Sparen Sie also da, wo es niemandem weh tut: bei den Materialkosten!
Die heutige Situation auf dem Rohstoffmarkt ist durch starke Preisschwankungen, stetig steigende Kosten und Versorgungsunsicherheiten gekennzeichnet. Das macht einen effizienteren Umgang mit Materialien notwendig. Wie stark die veränderten Bedingungen auf die Unternehmen Einfluss nehmen, wird besonders deutlich, wenn man die Kostenstruktur betrachtet. Die Materialkosten stellen in vielen Industrieunternehmen den größten Kostenblock dar, wie Abbildung 16 zeigt.
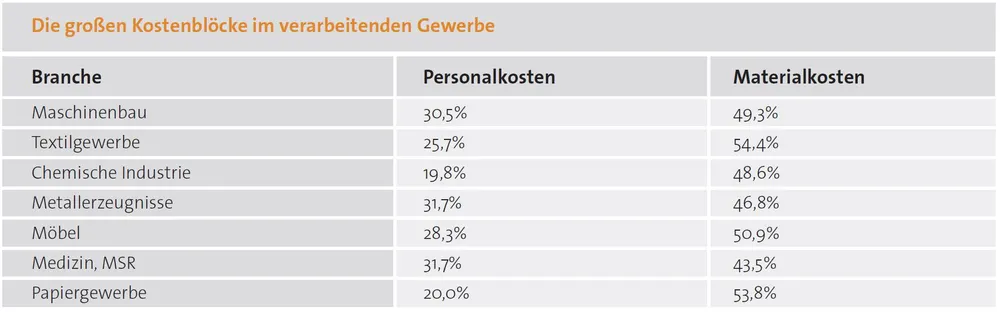
Es liegt nahe, die Materialkosten durch strategischen Materialeinkauf zu senken. Unter strategischem Materialeinkauf versteht man beispielsweise folgende Aufgaben:
- Beobachtung der Rohstoffmärkte und Rohstoffpreisentwicklungen
- Lieferantenauswahl, Lieferantenentwicklung und Lieferantenbewertung
- Verhandlung von Preis-, Zahlungs- und Lieferbedingungen
- Standardisierung von Beschaffungsvorgängen
- Analyse des Einkaufsverhaltens der Wettbewerber
- Bündelung von Einkaufsmacht
Unnötige Materialkosten entstehen aber auch, wenn zum Beispiel ein zu teures Material gewählt wurde, Ausschuss oder Materialverschnitt anfällt oder wenn durch die Materialwahl aufwendige Bearbeitungsschritte oder kostenintensive Lagerungen notwendig sind. Starke Einflussgrößen sind die Produktgestaltung, die Fertigungsverfahren, die Materialwahl und die damit einhergehende richtige Lagerung.
Wird bei der Optimierung durch Einzelmaßnahmen jedoch zu wenig auf die Auswirkungen auf andere Bereiche geachtet, zeigt sich häufig nur ein kurzfristiger Erfolg. Einen größeren und vor allem nachhaltigeren Erfolg erzielen Sie durch Veränderungen entlang der Wertschöpfungskette (Abbildung 17).
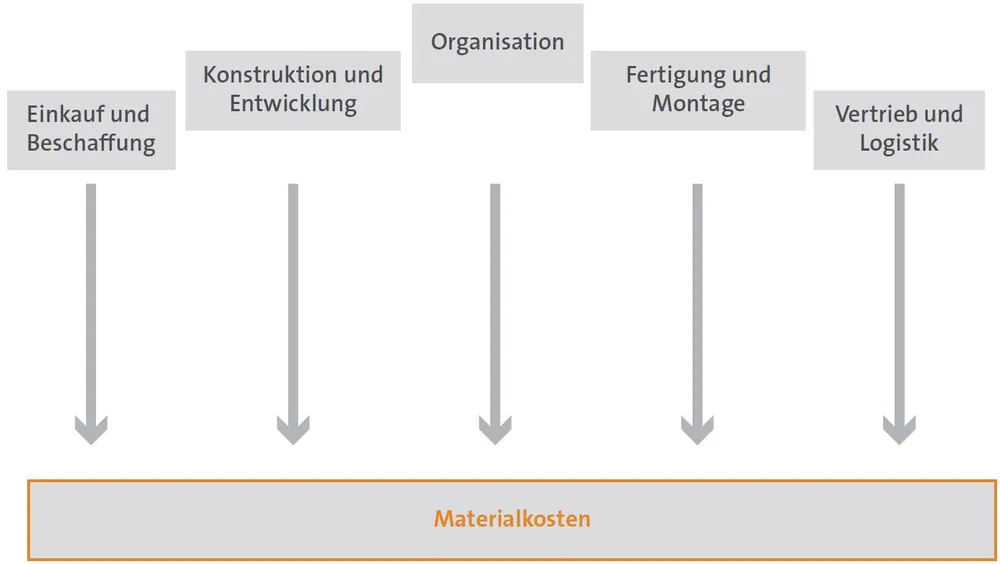
Betrieblicher Einfluss auf die Materialeffizienz am Beispiel Konstruktion und Entwicklung
Der Materialverbrauch und die Materialkosten werden bereits in der Konstruktion und Entwicklung der Produkte maßgeblich beeinflusst. Für einige Rohstoffe werden sich Engpässe und unkalkulierbare Kostensteigerungen ergeben, die bereits bei der Entwicklung neuer Produkte zu beachten sind. Die Recyclefähigkeit von Produkten und die Substitution solcher begrenzter Materialien sind ein wichtiger Aspekt für die Konstruktion und Entwicklung.
Beantworten Sie bereits bei der Entwicklung neuer Produkte solche Fragen wie:
- Ist die Versorgung mit den eingesetzten Materialien über den gesamten geplanten Produktionszeitraum gesichert?
- Welche Lösungen können versorgungskritische Stoffe ersetzen?
- Können recycelte Materialien oder Komponenten verwendet werden?
- Wie viel Energie verbrauchen die Produktion und der Gebrauch der Produkte beim Kunden?
- Wie kann das Produkt recycelt werden?
Die Kosten für Änderungen in der Entwicklungsphase sind vergleichsweise gering. Wenn allerdings Veränderungen am Produkt im weiteren Verlauf der Prozesskette durchgeführt werden müssen, dann können Ihre Kosten schnell explodieren. Um die Entstehung von Kosten durch Folgefehler möglichst gering zu halten,
- verringern Sie die Komplexität der Bauteile,
- führen Sie Standardisierungen und Modulstrategien ein,
- veranlassen Sie frühzeitige Abstimmungen zwischen Beschaffung (Einkauf), Produktion und Entwicklung.
Für die Produktion ist es wichtig, dass ein Produkt einfach zu fertigen ist, ein leicht zu verarbeitendes Material eingesetzt und der Verschnitt möglichst gering gehalten wird. Dabei ist auch die Produktqualität zu berücksichtigen, vor allem im Hinblick auf die Zahlungsbereitschaft des Kunden. Der Einkauf prüft, ob alternative Materialien in Frage kommen, und die Entwicklung prüft, welche Auswirkungen sie auf die Produktgestaltung haben.
Unnötige Produktionskosten entstehen in der Konstruktion, wenn das Produkt zu aufwendig konstruiert wird. Deshalb verfahren Sie nach der Devise: Je niedriger der Komplexitätsgrad, desto geringer ist auch der Verarbeitungs- und Organisationsaufwand. Zusätzlich wird auf diese Weise die Fehlerrate in der Produktion reduziert und die Teile- und Produktqualität gesteigert. Setzen Sie sich deshalb konsequent für die Verbesserung der Zusammenarbeit von Konstruktion und Produktion ein und berücksichtigen Sie die Belange der Materialwirtschaft.
Beschaffung
Um bei der Materialbeschaffung das materialwirtschaftliche Optimum zu erreichen, sind viele auf Erfahrungswerten und methodengestützten Planungen basierende Managemententscheidungen notwendig. Insbesondere Industriebetriebe werden zunehmend in ihre Einkaufsentscheidungen das Versorgungsrisiko für relevante Materialien und unkalkulierbare Materialpreisentwicklungen, die Sie gegebenenfalls nicht an die Kunden weitergeben können, einbeziehen müssen.
Sie können selbst bestimmen,
- welche Eigenschaften (Art, Qualität) die zu beschaffenden Materialien haben müssen, um das festgelegte Produktionsprogramm zu realisieren;
- welche Mengen pro Materialeinheit/ Materialgruppe beschafft werden sollen, damit der quantitative Materialbedarf gedeckt werden kann;
- den Zeitpunkt der Materialbeschaffung vor dem Hintergrund von Preisnachlässen bei vorzeitiger Bestellung/Beschaffung, unter Beachtung von Verfügbarkeit und gegebenenfalls weiterer Preissteigerungen und der bis zum Einsatz in der Produktion anfallenden Lagerkosten;
- die Art und Weise des Transports vom Lieferanten zum Werk und innerhalb der Produktion.
Grundsätzlich müssen Sie bei diesen Entscheidungsproblemen eine kostenoptimale Lösung für die Kombination der Varianten Beschaffung und Lagerhaltung finden. Möglicherweise müssen Sie auch über die Finanzierung der zu beschaffenden Materialien aus Eigenmitteln oder mit Fremdkapital entscheiden (s. Fandel/Fistek/Schütz, Produktionsmanagement, S.358–360).
Materialflusskostenrechnung
In der Produktion entstehen Reststoffe, Verschnitte, Abfälle, Abwasser und Emissionen, oder allgemein: Materialverluste, die Sie verwerten, gegebenenfalls intern wieder einsetzen oder extern entsorgen können. Herkömmliche Kostenrechnungssysteme geben nur begrenzt Auskunft über die Kosten von Materialverlusten.
Alles, was ein Unternehmen an Materialien verlässt, ist zuvor beschafft worden. Dazu kommen Transport und Lagerung, die Bearbeitung der Materialien und die Beanspruchung von Produktionskapazitäten. Berücksichtigt man diese Kostenbestandteile und ordnet sie als „Verursacher“ den Materialverlusten zu, dann können sie sich zu beachtlichen Beträgen summieren. Die Materialflusskostenrechnung zeigt,
- wo und bei welchen Materialverlusten im Unternehmen hohe ökonomische Einsparpotenziale bestehen,
- welche versteckten Kosten an den Materialverlusten hängen, die aber an ganz anderer Stelle im Unternehmen auftreten,
- um wie viel die Produktivität des Unternehmens erhöht werden könnte, wenn alle Materialverluste verringert werden,
- wie sich technische Maßnahmen zur Verringerung der Materialverluste tatsächlich amortisieren. (s. im Einzelnen Schmidt, M.: Materialflusskostenrechnung, 2011)
Förderprogramme zur Materialeffizienz
Das Bundesministerium für Wirtschaft und Technologie (BMWi) hat 2006 das sogenannte Impulsprogramm Materialeffizienz aufgelegt, mit dem die Beratung von Unternehmen zum Thema Materialeffizienz gefördert wird. Die Förderung erfolgt seit Mitte des Jahres 2011 über die Innovationsgutscheine des BMWi, Programmkurzname go-Inno, Modul go-effizient. Aktuelle Informationen finden Sie jederzeit unter:
- © FabrikaCr / iStock.com – Header_Website_1460_360_magazin.jpg
- © RKW Kompetenzzentrum – 20151208-Abb.15-Produktivitaetswirkungen-des-Handlungsfelds-Materialwirtschaft.JPG
- © RKW Kompetenzzentrum – 20151208-Abb.16-Kostenstruktur-im-verarbeitenden-Gewerbe.JPG
- © RKW Kompetenzzentrum – 20151208-Abb.17-ansatzpunkte-fuer-Materialeinsparung-entlang-der-Wertschoepfungskette.JPG